In the intricate world of industrial manufacturing, where every cut must be precise and every operation optimized for efficiency, the choice of tools can make all the difference. Circular slitter blades, with their ability to slice through various materials with accuracy and speed, are indispensable assets in numerous industries ranging from paper and plastics to metals and textiles.
However, to elevate their performance and extend their lifespan, manufacturers often turn to specialized coatings. Let's delve into the realm of coatings for industrial circular slitter blades and understand how they impact cutting performance.
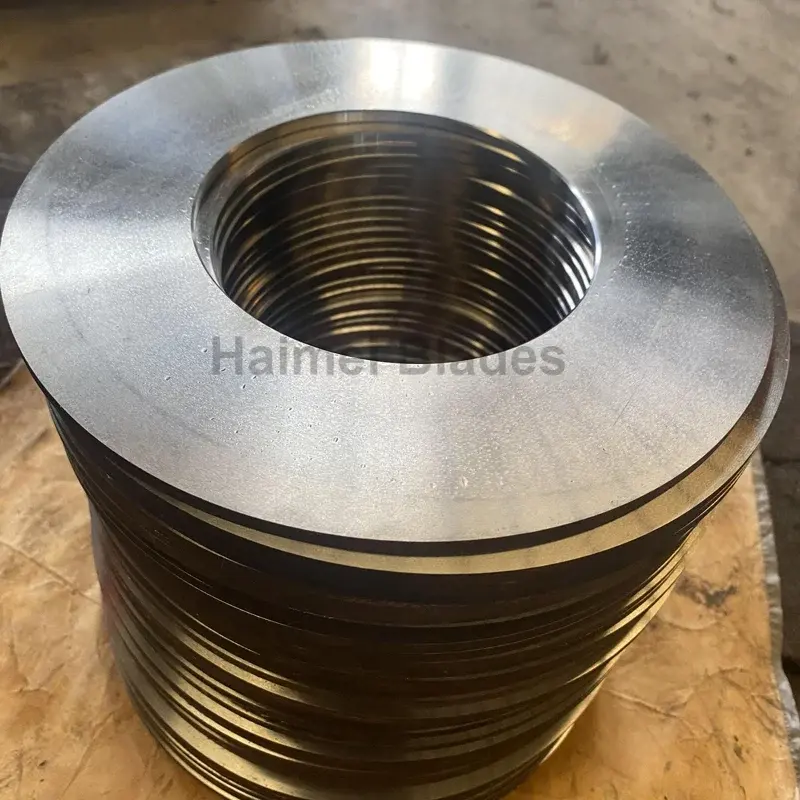
Understanding Circular Slitter Blades
Circular slitter blades are cylindrical cutting tools designed to slit, trim, or shape materials with precision. They come in various sizes and configurations to accommodate different cutting tasks and materials. Whether it's converting rolls of paper into smaller widths, trimming excess material in packaging, or creating intricate shapes in textiles, circular slitter blades are vital components in manufacturing processes.
Importance of Coatings
While the base materials of circular slitter blades, such as high-speed steel or carbide, provide inherent strength and sharpness, they are susceptible to wear and corrosion over time. Coatings serve as protective layers, enhancing blade performance and durability. Additionally, coatings can reduce friction, prevent material buildup, and improve cutting precision, resulting in cleaner cuts and smoother operations.
Types of Coatings
1. Titanium Nitride (TiN): TiN coatings are renowned for their hardness and wear resistance. They are suitable for cutting abrasive materials like cardboard, plastics, and non-ferrous metals. TiN coatings also reduce friction, ensuring smoother cutting action and prolonged blade life.
2. Titanium Carbonitride (TiCN): TiCN coatings offer a balance of hardness and toughness, making them ideal for high-speed cutting applications. They are particularly effective in machining tough materials like stainless steel and titanium alloys, providing excellent wear resistance and thermal stability.
3. Titanium Aluminum Nitride (TiAlN): TiAlN coatings exhibit exceptional thermal stability and oxidation resistance. They are well-suited for cutting heat-resistant alloys and hardened steels. TiAlN coatings enhance tool life and performance in demanding cutting conditions.
4. Diamond-Like Carbon (DLC): DLC coatings combine hardness with low friction and chemical inertness. They are suitable for cutting abrasive materials and high-speed machining applications. DLC coatings reduce material adhesion and improve chip evacuation, minimizing tool wear and maintenance requirements.
Impact on Cutting Performance
The choice of coating significantly influences the cutting performance of circular slitter blades:
- Extended Tool Life: Coatings like TiN, TiCN, and TiAlN enhance blade durability, reducing the frequency of blade replacements and downtime.
- Improved Cutting Precision: Coatings with low friction properties, such as DLC, promote smoother cutting action and minimize heat generation, resulting in cleaner cuts and enhanced dimensional accuracy.
- Enhanced Chip Evacuation: Coatings that reduce material buildup, such as TiN and TiAlN, ensure efficient chip evacuation, preventing chip jamming and maintaining cutting efficiency.
In the competitive landscape of industrial manufacturing, where efficiency and precision are paramount, the choice of coatings for circular slitter blades can make a significant difference. Whether it's TiN for abrasive materials, TiCN for high-speed applications, TiAlN for heat-resistant alloys, or DLC for extreme conditions, each coating offers unique benefits that enhance cutting performance and prolong blade life. By leveraging the right coating technology, manufacturers can optimize their cutting processes, reduce costs, and maintain a competitive edge in today's dynamic market.